Is CO2 Giving Ammonia a Run for Its Money in the World of Industrial Refrigeration?
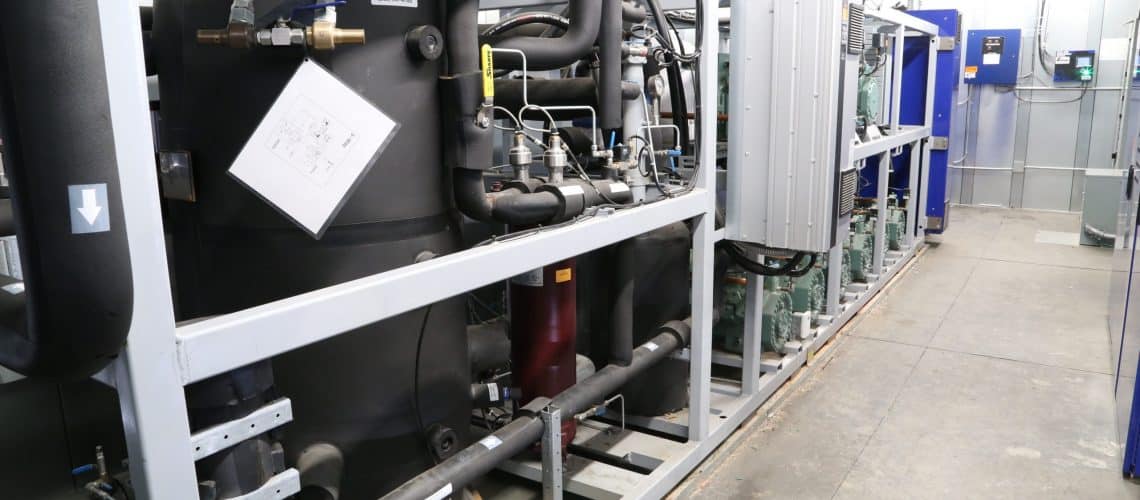
Since the early 1900s, ammonia has long been used as a major refrigerant in industrial refrigeration. Due to its thermodynamic properties, ammonia (NH3, R717) is used as a common refrigerant for large-scale, industrial applications and considered as a foundation for food processing and cold storage.
As the use of natural refrigerants evolves, and through the advancement of technology in the refrigeration industry, several countries and multi-national companies are now seeing the great potential of CO2 as a refrigerant in industrial refrigeration.
CO2 systems have been traditionally designed for commercial refrigeration applications; however, here are some of the reasons why CO2 has great potential to be a leader in industrial refrigeration as well:
- CO2 Is Safe for Industrial Applications – Since CO2 is classified as an A1 refrigerant, it has an Ozone Depletion Potential (ODP) of zero and a Global Warming Potential (GWP) of 1—all of which means it has zero impact on the destruction of earth’s atmosphere. But in addition to its neutral effect on the environment, CO2 is also safe to use in industrial refrigeration. Recent advancements push CO2 as a viable alternative refrigerant for industrial systems on the lower end capacity range of various industrial applications. Ammonia’s use in industrial refrigeration is limited due to its safety, toxicity, and flammability challenges. However, with CO2 being non-toxic and non-flammable, it is a great solution for systems where the use of ammonia is limited.
- CO2 Can Be Used in Cascade Systems – A CO2 cascade system that uses ammonia as a primary refrigerant and CO2 as a secondary refrigerant promotes high efficiency, especially in low-temperature applications. A CO2 cascade system is suitable for cold storage and food processing.
- CO2 Can Be Used in Transcritical or Subcritical Systems – A CO2 transcritical system is suitable for many industrial applications. Whereas, for some larger industrial projects, a CO2 subcritical system, whose high-pressure side of the system operates below the critical point, is more applicable and offers higher efficiency and more cost-effective option.
- CO2 is Future-proof – Aside from the energy and cost-saving benefits, C02 is immune from future refrigerant regulations. CO2 future-proofs your business as looming government refrigerant regulations only target synthetic refrigerants known to have harmful effects on the environment.
What Does This Mean for Food Retailers?
As the demand for different food products and online grocery orders continues to surge, growing concerns on how retail can manage order fulfillment continue to mount within the industry. To answer this problem, food retailers are leaning towards creating their own fulfillment centers to expedite grocery orders. The use of a CO2 system in industrial applications makes it possible and practical for food retailers of all sizes to build fulfillment centers, food processors, and cold storage infrastructures. With a team of experts trained to handle CO2 for industrial refrigeration, small- or large-format stores can adopt CO2 systems safely and efficiently.
Just like any other refrigeration system, the successful use of CO2 will ultimately depend on the design, strategy, and implementation to meet critical process requirements. CO2’s usage for industrial refrigeration is a promising step towards a more sustainable future.